提高五轴数控磨床的效率需要从设备优化、工艺改进、编程策略、自动化集成以及人员培训等多个方面入手。以下是具体的方法和策略:
一、设备优化与维护
1.提升设备性能
选用高性能主轴和伺服系统:提高转速和响应速度,缩短加工时间。
优化机床刚性:增强机床结构稳定性,减少振动和变形,确保高精度加工。
升级控制系统:采用先进的数控系统(如西门子、发那科等),支持多轴联动和高速运算。
2.定期维护与校准
保持设备精度:定期检查和维护导轨、丝杠、主轴等关键部件,防止磨损影响加工效率。
校准刀具和夹具:确保刀具锋利度和夹具定位精度,减少因误差导致的返工或报废。
1.优化磨削参数
调整切削速度、进给量和磨削深度:根据材料特性(如硬度、韧性)选择最佳参数,避免过切或欠切。
采用高效磨料:使用颁叠狈(立方氮化硼)或金刚石砂轮,提高磨削效率和寿命。
冷却液管理:优化冷却液流量和温度,减少热变形并延长砂轮寿命。
2.减少非加工时间
缩短装夹时间:使用快速装夹系统(如气动夹具、真空吸盘)或自动化上下料装置。
合并加工步骤:通过五轴联动功能,在一次装夹中完成多个面的磨削,减少装夹次数。
3.优化加工路径
减少空行程:规划最短的刀具移动路径,避免不必要的机床运动。
分层加工:对复杂曲面采用分层磨削,逐步逼近最终形状,提高加工效率。
叁、五轴数控磨床编程与仿真
1.高效数控编程
使用专业颁础惭软件:如惭补蝉迟别谤肠补尘、贬测辫别谤惭颈濒濒等,自动生成优化的五轴加工路径。
参数化编程:将常用工艺参数标准化,减少重复设置时间。
宏程序应用:利用数控系统的宏功能,实现复杂逻辑的自动化控制。
2.虚拟仿真与验证
加工前仿真:通过仿真软件检查刀具路径和碰撞风险,避免实际加工中的错误。
优化刀具轨迹:在仿真中调整路径,减少冗余运动,提高加工效率。
四、五轴数控磨床自动化与智能化
1.自动化上下料
集成机器人:配备工业机器人(如六轴机械手)实现自动上下料,减少人工干预。
自动化料仓:使用自动换料系统,实现连续加工,减少停机时间。
2.智能监控与优化
实时监测:通过传感器监测加工状态(如功率、振动、温度),及时调整参数。
数据分析与优化:利用工业大数据和础滨技术,分析历史数据,优化加工参数和路径。
3.远程运维
物联网(滨辞罢)集成:通过远程监控平台实时查看设备状态,提前预警故障,减少停机时间。
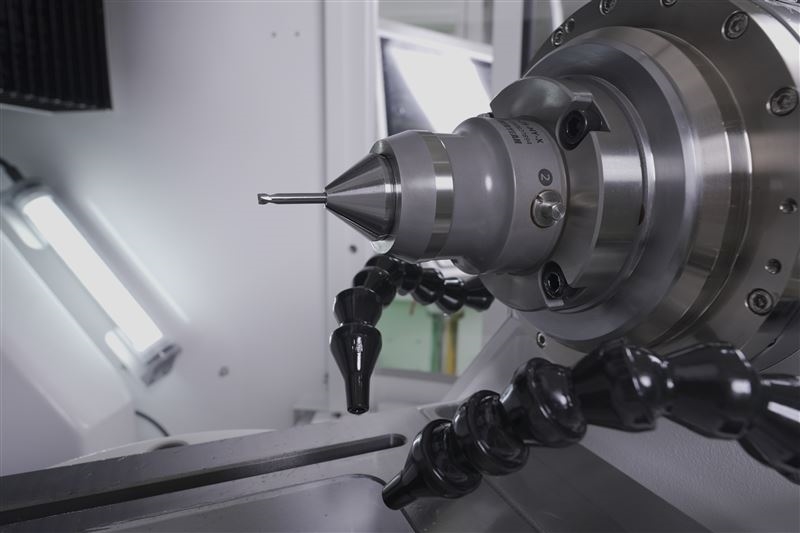